The diamonds we’re talking about aren’t the same as those in engagement rings or tennis bracelets. These are utilitarian gems. And they’re helping relieve the pain inflicted by degenerative disc disease.
Traditionally, the disc replacements created for these patients are made from plastics or metals. But Dymicron’s disrupting the industry with a cheaper, more durable solution: Triadyme®-C, a revolutionary total disc replacement for the cervical spine. Using a tri-lobe design, this artificial disc is molded from human-made diamond that never wears out (💎 really are forever). Drill
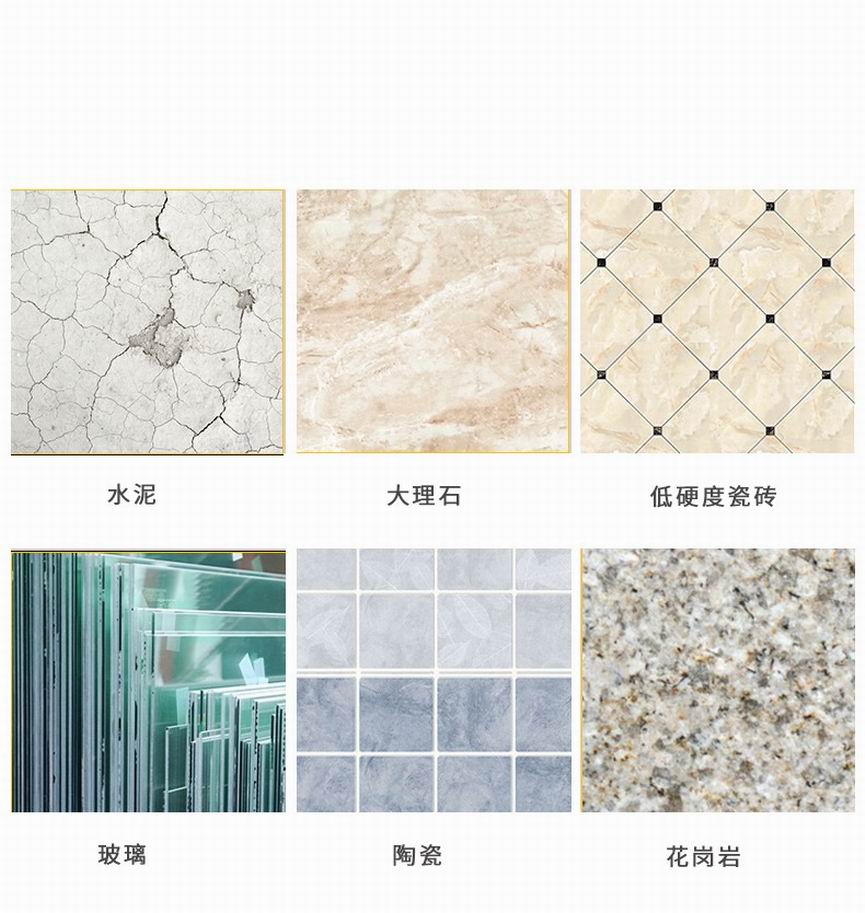
The Triadyme®-C disc replacement shows powerful potential: It’s already available outside the US and on its way to FDA approval stateside. We spoke with Dymicron Chief Strategy Officer Ted Bird to learn how these dazzling diamonds are reshaping the $1b cervical implant market—and how you can invest and help them reach spines in need.
This interview has been edited and condensed for clarity.
Dymicron’s founder, Dr. Bill Pope, was an expert in polycrystalline diamond, the hardest material known to humankind. He discovered the destructive health effects of joint replacement wear debris when a neighbor mentioned he needed a revision operation on his total hip replacement. And that’s when the lightbulb turned on. Pope realized if he made implants from polycrystalline diamond, no one would need additional operations because theirs would never wear out.
The Triadyme®-C implant eliminates the primary long-term issue with traditional disc replacements: wear debris. But beyond that, additional degeneration can develop if the motion of an artificial disc doesn’t closely align with a patient’s natural movement.
In a leading spine biomechanics lab and clinically in over 500 patients outside of the US, we’ve shown that our disc replacement’s motion mimics a normal disc’s center of rotation without any wear or dislodgment of the product. No other disc on the market can provide this combination of zero wear debris and the exceptional biomechanics that our innovative tri-lobe design offers.
We’ll continue to build clinical data, but we plan to partner with or sell the Triadyme®-C disc to a larger company with the infrastructure to provide this best-in-class solution to the largest number of patients. Well-known, large medical device companies like Johnson & Johnson, Stryker, and Medtronic aren’t innovating and developing next-generation products themselves. They generally look to companies like Dymicron for these solutions so they can partner or acquire to distribute them.
Morning Brew delivers quick and insightful updates about the business world every day of the week from Wall St. to Silicon Valley.
While our current efforts are 100% focused on achieving FDA market approval for our cervical discs, the incredible benefit of our product for other orthopedic and artificial joints isn’t lost on us. With the appropriate design, there’s potential for this product in the lumbar spine, hips, knees, elbows, and anywhere you have an articulating joint that degenerates or needs an implant. We have the patents for the entire human body, so we own the space. The potential to develop elsewhere is clearly there.
The FDA process is quite expensive and long. Generally, venture capitalists and institutional investors don’t like long processes and often worry about the risks associated with an FDA trial. Because of that, many innovative medtech and med-device companies have to turn the lights off when they can’t get the funding they need.
That’s the exciting part of what the SEC and Congress have done with the Jumpstart Our Business Startups Act. It created equity crowdfunding opportunities so we can raise capital through interested retail investors. Now we can generate a whole new fan base of interested people and bring on investors who can help us solve the problem of degenerative disc disease.
Each Triadyme®-C implant is made with natural diamond particles ranging from 4 to 8 micrometers in size (the equivalency of 0.005 carats). So you’re not going to impress a future spouse with those.
But during manufacturing, we fuse millions of these tiny carat particles into a mold within a massive 60-ton diamond press. The result is a solid polycrystalline diamond that, with our largest-sized implant, is the equivalent to 5.75, almost 6 carats. And that’s a diamond worth noticing.
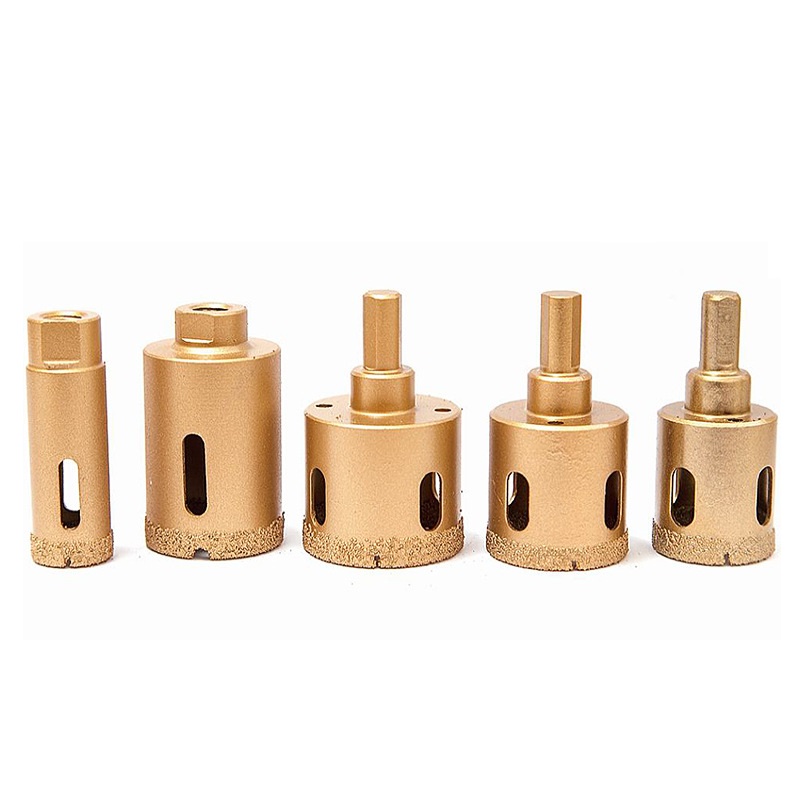
Center Drill Bit Morning Brew delivers quick and insightful updates about the business world every day of the week from Wall St. to Silicon Valley.