Oil grooves are used to lubricate the inside of a bearing, and can come in many forms — from a single hole that takes a few drops of oil, to helical patterns that distribute it over the entire internal surface. The ideal arrangement is a looping figure eight pattern similar to an oscilloscope Lissajous figure, but cutting these is a nightmare. That is, unless you’ve got the proper tool.
We figure [Machine Mechanic] must need to cut a lot of them, as they spent quite a bit of time perfecting this custom lathe attachment to automate the process. Through an assortment of clever linkages and a rod-turned-crank that was welded together in-situ, the device converts the rotational motion of the lathe into a reciprocating action that moves the cutting tool in and out of the bearing. Incidentally the business end of this gadget started life out as a bolt, before it was turned down and had a piece of tool steel brazed onto the end. Screw Actuator
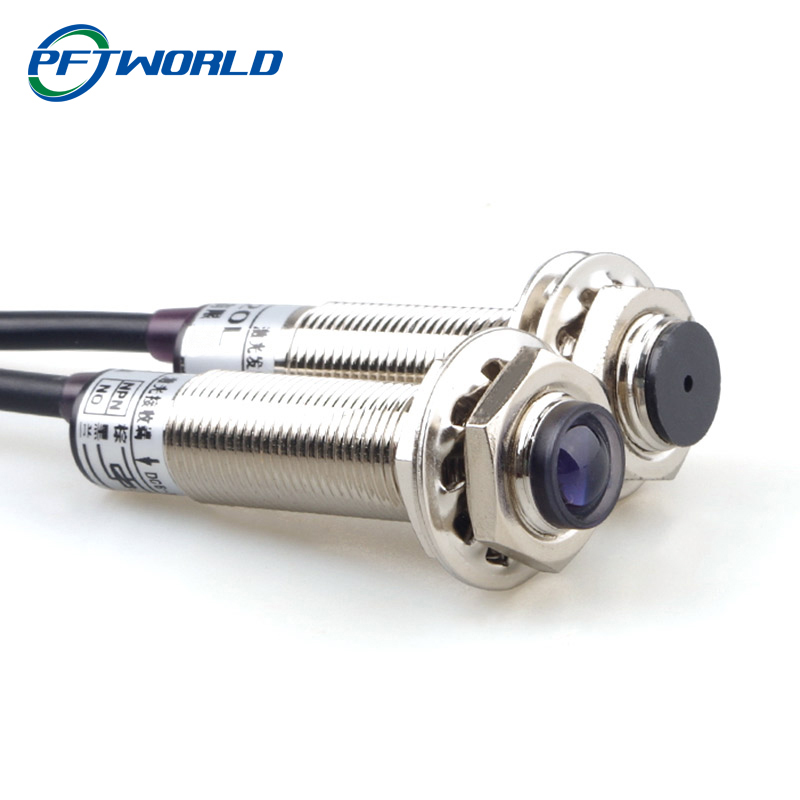
With a little adjustment, it seems like this device could also be used to carve decorative patterns on the outside of the workpiece. But even if this is the only trick it can pull off, we’re still impressed. This is a clever hack for a very specialized machine shop operation that most would assume you’d need a four-axis CNC to pull off.
Lathes seem at first like rather single purpose machines, we’re always pleased to discover strange and wonderful things being done with them, like this seemingly impossible-to-turn piece, and this combo wire EDM and lathe.
Thanks to [Zane] for the tip.
Great ingenuity! Sure it’s quite hazardous but I’m sure they understood that. Also, I like that they didn’t weld directly onto the chuck, despite what Mr happy’s comment above says.
It is a very smart hack and if you payed attention he does not weld to the lathe chuck at all see 8:27. And my grinder never has the guard attached because I grind vehicles mostly in hard to reach places. Just wear safety equipment and know how to handle power tools.
Good job on finding this @hackaday.
Exactly, good idea but very very bad execution…
That’s ironic. A YouTube notification came through a few days ago about Thang creating an animation from this same video. https://youtu.be/KE4o8WometM Easy to understand what’s going on now! 👍
Why couldn’t a two axis cnc lathe do this no different then I ID thread with the wrong pitch… or am I missing something else?.
A 2 axis would have no problem.
Sure, but he doesn’t seem to have a 2-axis CNC lathe.
No. Actually you would need full 3 Axis CNC lathe. At which case you would most like be looking at a machine with ‘Live Tooling’. These are machines that can do normal lathe work plus the addition of some milling work. They tend to get significantly pricier. You would need to do a lot of oil grooves to justify one.
Most 2 Axis only have an X and a Z axis (tool in/out and back/forth movement). They do not have programmable control over the chuck orientation for any given tool movement. Hence you would not be able to track and do multiple passes required to cut the groove.
What about threading? Yes its true most of these machines have an encoder connected to the spindle to allow for threading. Threading is done using special built in subroutines which ends up limiting the control a machinist has. Don’t get me wrong, these subroutines are very versatile. But they all require a constant pitch. These oil grooves have a constantly changing pitch.
Would there be anything technically limiting a CNC controller manufacturer from adding special subroutines that could do this? Probably not. Its just I haven’t seen anything on the machines I use (vintage early 2000’s).
You could cut this on a 2 axis as long as at has c axis functionality. I used a machine like that at my last shop, though, admittedly, it did have live tooling without a y axis.
I do get your point though, a lot of 2 axis machines don’t have c axis functionality.
I am basing my statement on an oddball machine.
Your assessment is correct, I have done this type of groove before on lathes that had live tooling capability but only because they had c-axis ability
I do find the main video here quite interesting it’s a cool solution to a problem. Another way of doing it is to create a straight plunge Groove near the ends at front and back and then just connect them with a fast pitch helix programmed like a large pitch screw thread connecting them. It doesn’t have to be a figure 8 style like this.
Yeah. I’ve been hypercritical of these videos in the past and Hackaday for even promoting them. There was a video a while back about fixing a rickshaw axle or something and the entire comments section was about what a terrible idea and how unsafe the “hack” was. This video: No eye protection at all. One dude is wearing sandals. I understand this comes from some developing nation, and exhibits a bit of ingenuity but that is it. The total disregard for even the most basic safety considerations is an example of what not to do. You would not be allowed into a junior highschool wood shop looking like that let alone any modern shop with even a modicum of interest in worker safety. It is also bizarre that they cannot afford a single tool bit and do all the precision work on a dirt floor but have somehow gained access to multi-ton machine tools. These priorities are not to be promoted.
Multi-ton Machine tool is startup CAPEX. Might have been bought decades ago when the company was rich, or might be on a loan they’ll never pay off.
Safety equipment, tool bits, maintenance, replacing broken guards, etc are running costs, which they maybe can’t afford now, or the bean-counters won’t allow them to spend on.
This is how everyone used to work. Get over it.
Won’t somebody please think of the children!!! I doubt that this post is going to cause an epidemic of college teachers telling students they should run their lathes in sandals. The safety handwringing seems more like an excuse for commenters to express their distaste for poor people and the aesthetics of poverty under the guise of “safety concerns”. If some YouTuber named Machining Greg did the same project in sandals but the camera was a DSLR on a tripod I bet fewer people would be so “concerned”.
He welded a longer bar to the lathe tool, not the lathe chuck itself. I still cringed when I saw him welding above the lathe though. The video did give me the urge to make my own version of the tool, so I’m glad Hackaday linked to it. Sometimes demonstrating a concept and sparking an idea is all that’s needed.
I have been reading Hackaday for more than a decade, and I come here for the ideas, the projects, and the tools and techniques. Much of what’s posted is uninteresting to me, but regularly something is covered which sparks my imagination or expands my conception of what’s possible.
I strongly disagree with the safety-puritans in this thread (and elsewhere) arguing for censorship. Information should be spread, that’s the point of this site and the internet basically. The cultivation hackaday already engages in enables them to create a high density stream of technically interesting information. Adding “safety constraints” to the scope of coverage would degrade, not improve, that coverage.
The simple solution for projects with “insufficient safety practices” (by at least someone’s standards) is for that self-appointed high priest of safety to comment with better practices on the post.
Keep posting Hackaday! This post itself was fairly interesting to me, and has made me start considering what low-cost modifications I might be able to make to my tools to enable better in-house machining.
I think an acknowledgement of the lack of safety practices is a good place to start for a hackaday post. Learning what not to do and why is almost better than showing a video with perfect safety practices that doesn’t address them. More often than not we, as hobbists, do not have access to machines with all the latest safety features and it is good to ensure people are aware of the risks and have truly engaged in thinking about them and are fully aware of what can happen if things go wrong. Those who cannot assess the dangers and act accordingly probably should not be allowed around a manual lathe. What a interesting stance to take that there could be a video that would be too dangerous to even look at. It sort of feels like your saying that videos of people working without safety equipment can’t be shown to rich idiots because they can’t be held responsible for their own safety. You expect hackaday to be their crossing guard and protect them from themselves. Summation: talking about dangers, safety practices, and even the fact that humans are not great at thinking about long term consequences=good, hiding anything that might be dangerous so no one even recognizes it=bad.
It’s sad to see people wanting to censor videos like this due to “lack of safety”. This is is a “hack” website and secondly, this is not a instructional video: this is a guy is showing how he does this. Sure, put a disclaimer in the text: This video doesn’t follow modern recommended safety advice. Please make sure you know what you’re doing.
But if you hurt yourself because you buy yourself an industrial power tool and mindlessly copy a guy in a video, I’m not sure any safety precaution would have helped you.
This video is a wonderful hack!
All you safety naysayers step aside and hear me out. The ability to make parts or machines with the most minimal of tools is simply awesome to behold. The lathe sounds horrible (bearings or gear whine) but to be able to build sleeve bearings with oil grooves is incredible. I’ve seen videos where a guy built a metal brake from angle iron. It was done with car batteries for the welder and all else done with a file and a power drill. I’ve seen videos of people cutting open refridgerator compressors repairing them and welding the housing back together with a “buzz box” welder. I live in the USA and yeah when I walk in to a machine shop it is temperature and humidity conntrolled with the machinery mounted to a concrete floor thats level to within .0005 inches. (the machine not the floor) Sometimes I think all the safety actually inhibits the inventive side of fixing a problem. I.e. I can’t do it this way cause it won’t be safe. Whereas some guy in sandals and a t-shirt just gets the job done. Kudos to that guy!!! (Even if he does have three fingers;)
Perhaps you got this website confused with ProperProcedureADay? Do you really need a lifeguard to tell you you shouldn’t be wearing sandals in a machine shop?
That would remove far to many good idea we should want to read about – this mechanism is superbly simple and elegant in concept, directly useful to many of us as another way to make something we may have to dig out for that tricky part in the future!
Also at just what level are you satisfied its proper health and safety approved? There is no such thing as perfectly 100% foolproof safe!
In many cases even with real care for health and safety the best practices are conflicting – like the wearing of protective gloves for holding stock around a machine – some scream its super dangerous and will rip your hands off etc when the glove snags, for others its the only sane thing to do because it gives you the protection to have a proper grip on the likely sharp stock, so its controlled and cant harm you…
This person clearly doesn’t have all the safety gear YOU would want – but its pretty apparent they have a clear understanding on the risks involved, as the functional device of that complexity isn’t your first project, heck the concept for it wouldn’t even exist if was, and yet despite wearing an OHS consultants nightmare they are entirely intact…
Oops, apparently I accidentally clicked on OSHAaDay
This is Hack-a-Day. Not an industrial safety symposium. A hack is, by definition, something that is not a standard industrial process. And don’t forget the colloquial use of the word hack to describe someone. It is certainly very reasonable for some to point out obvious safety issues. But it is not the responsibility of this web site to do a safety analysis of every hack they link to.
We appreciate your concern. We, however, don’t know everything about safety in all fields — nobody does.
Those of you who do know better could be doing the community a great service by simply saying what the OP did that was dangerous, and why, and proposing a mitigation strategy.
For instance, I know a great deal about laser safety, some learned from the FDA, but also a lot learned from friends and colleagues. I always try to promote the simplest and/or most effective strategies, which often round down to “thoughtfully terminate your beam, put in in a box, use a webcam if you need to see it” but could be much more involved in particular situations.
So that is our editorial policy: we don’t know everything, but we do what we can. We rely on _you_ to help us fill in the gaps.
That explains it. Reddit is the worst.
And boom every single article and video sourced from 3rd world countries was removed because of reddit safety whiners
Pointing out safety issues is alright, but god damn it Brian and Bob, bitching is not cool.
Thanks Hackaday. Great post. This is why I come to this site. Forget the critics, keep on posting
this man’s slave labor is building this comment section’s harbor freight tools and redditAday is most worried about him not having a guard on the grinder lmao. write your congressman and tell them to ban foreign made products and 3rdworld scab labor if you’re so mad about it.
I’ve really enjoying watching these types of videos of fabrication and fixing from other countries. As others have mentioned theres some great tips (hacks) that can be gleamed from watching them.
Plato wrote: “our need will be the real creator” – we do with what we’ve got or make it, or hack it, or save up and buy it (if thats a option), but for many people saving for your families daily food is the priority over efficiencies or equipment.
Why has censorship become such a knee jerk reactionary response in our society? Probably because the current leftist authoritarian establishment practices it so broadly and boldly their followers think it is okay. IT IS NOT! This guy did not follow the “safety rules” but he was creative as hell. Get over it. Many great ideas are censored nowadays because they don’t adhere to the establishment platform – that doesn’t mean they should not be heard. Grab your teddy bear, go to your safe place and leave we free peoples alone!
Please stop framing the world with grievance politics. I’m highly liberal and I drink whiskey while running a lathe on my own. I make my living as a machinist for a long time now. Your general gripe against people different than you is moot. Please take the political arguments elsewhere I don’t come here for that and neither does anyone else and we’re all sick of it.
If someone gets hurt because they’re stupid enough to do something they should know isn’t safe it’s their own fault. OSHA exists for a reason, and a lot of people have died from preventable things that often employers force on workers. I worked in a place where people died of heavy metal poisoning but this wasn’t even communicated to the workers as a possibility. The world is not your black and white Tucker Carlson confused face.
So he complains about leftist censorship and your response is to tell him your a liberal and then attempt to silence him?
I am sometimes appalled by the comments of certain people who are convinced that the world revolves around them and their rules.
You have to understand that there are countries where a pair of safety shoes costs the equivalent of several months’ wages. So yes, security may be an option in some countries.
On the other hand, using a lathe, a milling machine, even a simple cutter is dangerous if the users have no brains you can put all the warnings you want, an idiot or an inconsiderate will always find a way to put himself in danger.
Please be kind and respectful to help make the comments section excellent. (Comment Policy)
This site uses Akismet to reduce spam. Learn how your comment data is processed.

Cnc Milling Service By using our website and services, you expressly agree to the placement of our performance, functionality and advertising cookies. Learn more