Batteries for electric vehicles (EVs) need protection from harsh external conditions. Generally located on the underside of the vehicle, EV battery enclosures protect the cells from exposure to water, dust, debris, and other elements. Like other enclosures, EV battery enclosures also undergo temperature and pressure changes that can lead to problems without proper venting. But EV batteries present unique venting challenges including potentially dangerous thermal runaway conditions. Considering these challenges, integration of design, manufacturing, installation, and testing are crucial to optimal EV battery venting performance.
Numerous components in an EV require venting. Lighting, horns, electronics, powertrain, and other components all experience temperature changes resulting from weather conditions, moisture, or heat from electronic circuits. These temperature fluctuations produce pressure changes inside the components. Changes in altitude can also trigger pressure changes. A trek up Pike’s Peak, for example, could result in pressure changes of up to 140 millibars (2 psi). Agrochemical Eptfe Membrane
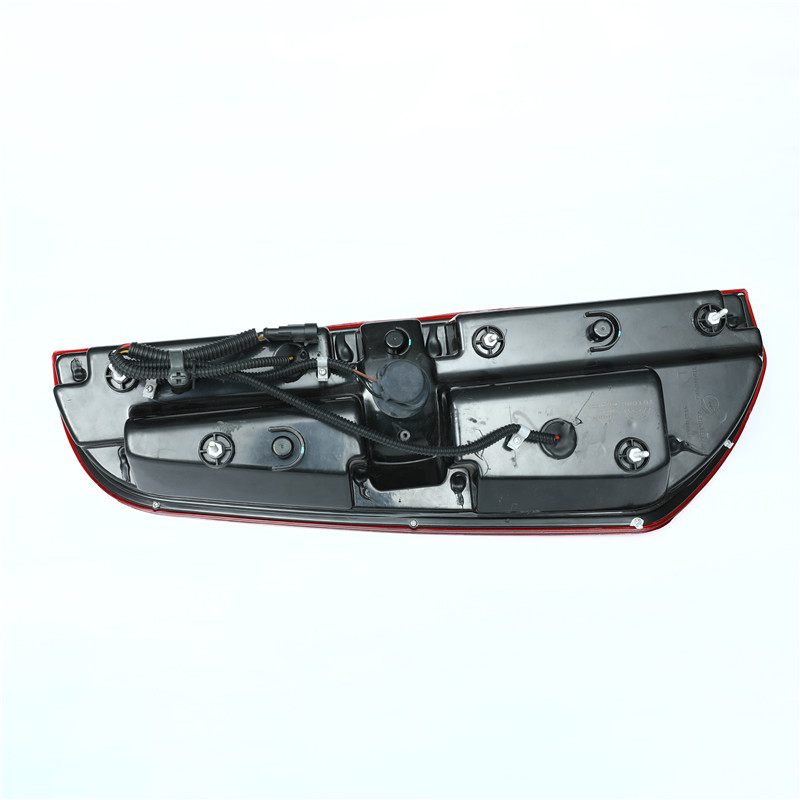
Expanded polytetrafluoroethylene (ePTFE) membranes have proven effective in venting EV enclosures and providing pressure equalization. This material allows gases to flow in and out of the enclosure but helps prevent liquid and particle contaminants from entering the enclosure.
Along with exposure to the various elements experienced by other automotive components, battery packs present additional challenges due to their location, size, and chemical makeup. Packs located on the undersides of vehicles can be exposed to water fording or submersion as a vehicle traverses standing water. Roadway water may include salt and other corrosive chemicals. Car washes can expose vehicles to high-pressure sprays of varying temperature. Dust, debris, and vibration can also impact the battery pack.
Perhaps the biggest challenge with EV battery packs is the potential for thermal runaway. If lithium-ion battery cells are damaged by puncturing, overcharging, manufacturing defect, or other causes, they can release gas and heat. This can trigger other cells to decompose, leading to a thermal runaway condition where rapidly increasing temperatures and pressures released by cells exceed the venting capability of ePTFE membrane vent. At this point, the vent is unable to allow gases to escape fast enough and additional pressure relief is needed to avoid rupturing the battery pack enclosure, which is typically made of lightweight materials to conserve weight.
Dual-stage venting provides an effective solution to the unique challenges of EV battery packs. The first stage — passive venting — handles gradual changes in temperature and pressure via the ePTFE membrane. The second stage — active venting — allows the vent to rupture and gases to quickly escape in a thermal runaway situation.
As an example, an enclosure that would rupture at a pressure of 1,500 millibars (21.7 psi) could be equipped with an active venting system that opens at 300 millibars (4.3 psi), well below the rupture pressure. Without active venting, the enclosure would rupture quickly.
With dual-stage venting, a single assembly can help accomplish both passive and active venting functions and assist in controlling the pressure and location at which gas is released. Typically located on the top or side of the enclosure, the vents can be situated to allow for controlled gas release, which helps mitigate risk by allowing the designer to determine the location of the release.
Ease of installation and efficiency in the manufacturing process are key to the overall battery pack solution, particularly if the packs will be manufactured on a high-volume basis. Different fittings are available, depending on enclosure materials. A bayonet quarter-turn fitting is most common, though threaded fittings are feasible with sufficient thickness of enclosure material. Drainage around the vent should also be provided to allow for runoff of water reaching the vent. Weight and cost also need to be considered in the solution. While vents can weigh less than 15 g (.53 ounce), they contribute to the overall weight and cost of the battery pack.
The number of vents required will vary depending on the application but common practice has been to provide at least two vents and up to 12 vents for full EVs and at least one vent for hybrid vehicles. Airflow needs will depend on free air volume and anticipated nominal operating pressures. An experienced venting partner can help analyze the battery pack and provide venting recommendations.
With venting a necessity in battery pack design, dual-stage venting efficiently provides both passive and active venting in one assembly. Proper venting, however, requires careful planning and integration in the overall process and should not be treated as an afterthought. To achieve successful solutions, vehicle and battery pack manufacturers should engage an experienced venting partner with the expertise and resources needed to analyze issues and develop precise solutions. The partner should have a proven track record, with solutions approved by other OEMs.
With a strong partnership engaging the expertise of the venting and battery pack manufacturers, dual-stage venting can contribute significantly to the successful production and operation of EVs.
This article was written by Jake Sanders, Supervising Engineering for the Venting Solutions team at Donaldson Company, Inc. (Bloomington, MN). Contact Sanders at This email address is being protected from spambots. You need JavaScript enabled to view it.; 952-703-4868. For more information, visit here .
Read more articles from this issue here.
Read more articles from the archives here.
4 Predictions for 2024: AI Set to Supercharge Robotic Automation
Reaching for the Moon: Astrobotic Peregrine Mission One
How Corning’s Hyperspectral Imaging in the Sky Sees the Unseen
Additive Manufacturing for Aerospace: Taking Your Production to New Heights
Hydrogen’s Promising Role in Heavy-Duty Vehicles
Here's an Idea: A New Minimally Invasive Approach to Spinal Cord Injury
Understanding Technological Advancements in IR Detection Modules
Reaching for the Moon: Astrobotic Peregrine Mission One
4 Predictions for 2024: AI Set to Supercharge Robotic Automation
How Webb Telescope Made Simulation Software Better
How Much Do You Know About Predictive Maintenance?
A Precision Arm for Mini Robots
Here's an Idea: A New Minimally Invasive Approach to Spinal Cord Injury
Here's an Idea: Human Factors in Drug Delivery
Here's an Idea: Powerful Sensors for the Eye
You may reach us at privacy@saemediagroup.com.
You may unsubscribe at any time.

Moisture Permeable Membrane © 2009-2024 SAE Media Group